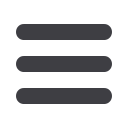
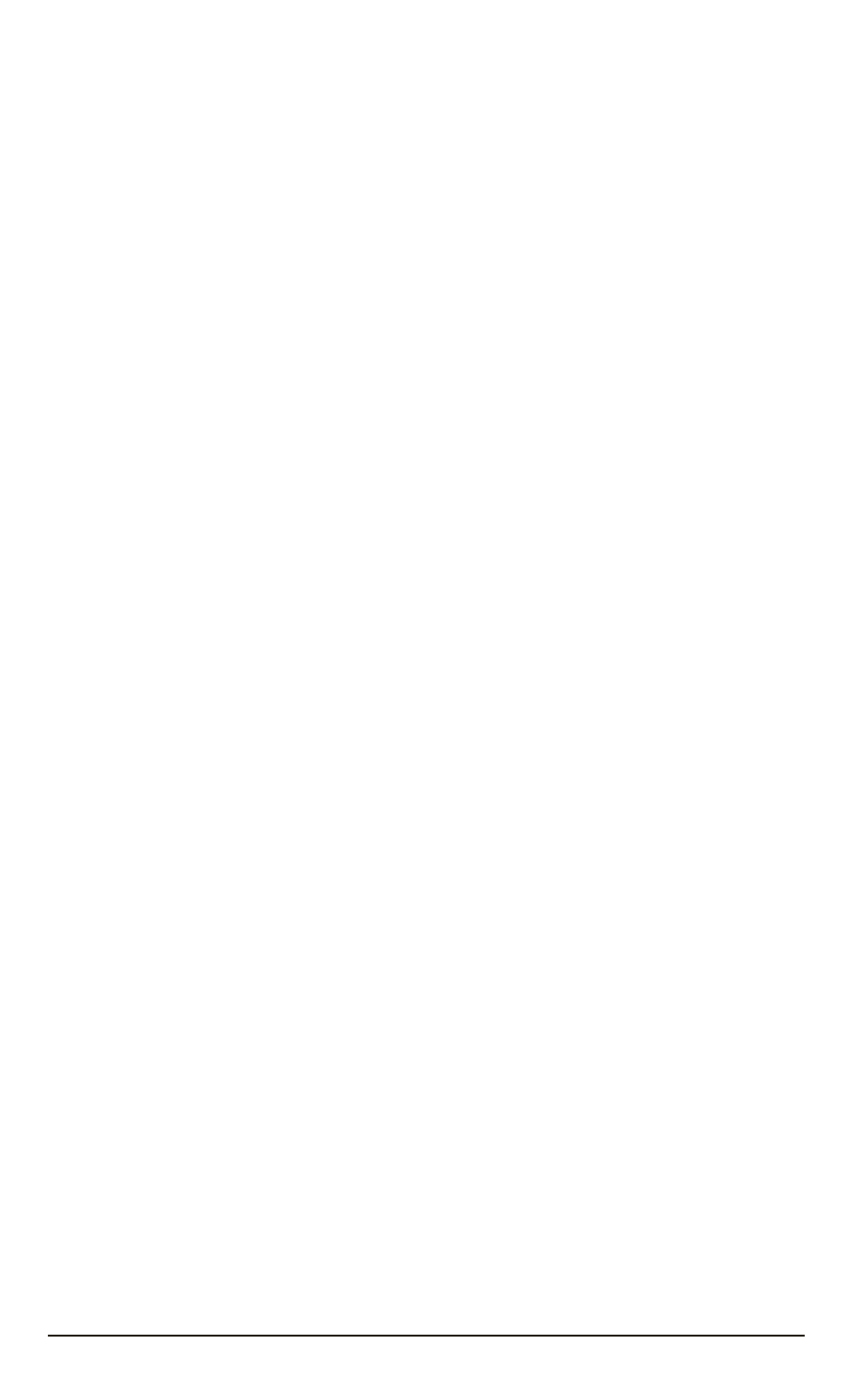
deployed shape. The proposed design is a space truss made of foldable composite
rods with thin-walled collapsible cross-section. The design structural integrity allows
the manufacturing of reflector as a single part made of carbon fiber reinforced
plastics with high specific strength and stiffness as well as low thermal expansion,
thus providing necessary rigidity and stability of the structure in wide temperature
range. All-composite design will additionally reduce the mass and will allow to avoid
composite-metal joining issues.
Keywords
:
large space structures, deployable space reflector, composite materials,
thin-walled structures, finite element modeling.
1. Introduction
Rising demands on space radio-communication and
Earth remote sensing satellites require the enlargement of aperture of
onboard antenna. At the same time, the lift capabilities of launch vehicles
are limiting significantly the payload mass and size, that’s why conventional
and advanced large space antennae structures are designed as deployable.
Large deployable antennae structures could be subdivided into different
types [1]: rigid petals with hinges forming the continuous reflecting
surface (RadioAstron, TRW Sunflower); textile reflecting surface held by
deployable support structure (ISS Reshetnev Loutch, Astromesh), inflatable
reflector and/or support system (Model-2, NASA IAE), hybrid concepts
and other (shape memory support structures, springback structures and
so on). The choice of antenna type for given spacecraft is based on the
required reflector aperture and operating wavelength. Typical root mean
square (RMS) of reflecting surface is higher for rigid type antenna and
lower for inflatable ones, contrariwise, stowage coefficient, the ratio of
characteristic dimension in deployed to transport position, is rising from
rigid to inflatable reflectors. The intermediate characteristics of RMS
and stowage coefficients of textile reflecting surface and truss support
antennae structures allows them to fill the gap between rigid and inflatable
reflectors. However, reflectors of this type usually consist of large amount
of mechanically jointed parts having their own freeplays and dimension
tolerances, resulting in high manufacturing and adjustment complexity.
Historically, composite materials with high specific stiffness and
strength properties are widely used in large space structures, providing
excellent performance characteristics along with significant weight savings,
but the field of their application is significantly limited due to, among
others, low reliability of composite joints. Therefore, most advanced
truss support structures are made of composite parts jointed together
with metallic ones. This solution partially eliminates the benefits of
composite material structure by increasing overall weight, decreasing
lowest eigenfrequency magnitude and introducing technological problems
with metal-composite joints.
Meanwhile, deployable structures based on furlable or bi-stable thin-
walled beams are studied [2]. Most of these structures are used as antenna
blade or straight support booms and masts. Structures of this type are
packed by flattening the beam’s cross section and further rolling it on the
50 ISSN 0236-3941. Вестник МГТУ им. Н.Э. Баумана. Сер. “Машиностроение”. 2015. № 1