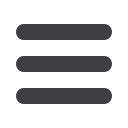

heights, as the increase in the height is determined only by hydraulic losses
of the whole channel,
k
D
=
D
1
+
h
D
1
+
h
3
is a correcting factor for the channel
mean diameter change, having little effect on the final result.
The height increase coefficient determined by finning in the turbulent
flow mode (
n
= 0
.
8
;
m
=
−
0
.
25
) will constitute
K
hf
= (
k
D
cos
β
)
−
0
.
583
×
×
t
+0
.
583
(
t
+
h
−
1)
0
.
417
(
t
−
1)
and, as it was shown above, it can
grow within the investigated range of parameters up to values 1.15. . . 3.5,
which should be taken into account when designing the chamber thermal
protection.
Conclusions.
By using the coplanar flows in the cooling channels, their
energy efficiency will be significantly increased with regard to the firewall
heat release, mostly due to the increase in the convective component
as compared to the conventionally finned channels with the insufficient
efficiency.
By changing such finning parameters as the fins intercrossing angle
2
β
,
the Biot number, the relative finning pitch ratio
h
1
within the reasonable
and acceptable bounds, the thermal hydraulic efficiency can be controlled,
as well as the desired level of heat release and the thermal state can be
achieved for the structure.
CC efficiency estimation with regard to the
K
Q
criterion can be based
on the previously developed methodology for the classic finned channels
allowing for the actual effective area of finning on the heat-releasing
surface.
REFERENCES
[1] Aleksandrenkov V.P. Efficiency of heat transfer intensification in circular finned
cooling circuits of combustion chambers.
Vestn. Mosk. Gos. Tekh. Univ. im. N.E.
Baumana, Mashinostr.
[Herald of the Bauman Moscow State Tech. Univ., Mech.
Eng.], 2013, no. 3, pp. 111–121 (in Russ.).
[2] Kudryavtsev V.M., Orlin S.A., Posnov S.A. Experimental research of flow resistance
in circuits with complanar channels.
Izv. Vyssh. Uchebn. Zaved., Mashinostr.
[Proc.
Univ., Mech. Eng.], 1983, no. 4, pp. 54–58 (in Russ.).
[3] Pelevin F.V., Il’inskaya O.I., Orlin S.A. Engineering application of coplanar channels.
Vestnik PNIPU. Aerokosmicheskaya tekhnika
[PNRPU Aerospace Engineering
Bulletin], 2014, no. 2 (37), pp. 71–85 (in Russ.).
[4] Orlin S.A., Posnov S.A. Experimental research of heat transfer and flow resistance
in circular ducts with complanar channels.
Trudy MVTU im. N.E. Baumana
[Proc.
Bauman MSTU], 1984, no. 417, pp. 9–12 (in Russ.).
[5] Kirillov P.L., Yur’ev Yu.S., Bobkov V.P., ed. Spravochnik po teplogidravlicheskim
raschetam. Yadernye reaktory, teploobmenniki, parogeneratory [Reference book
on thermal and hydraulic calculations. Nuclear reactors, heat exchangers, steam
generators]. Moscow, Energoatomizdat Publ., 1990. 360 p.
54
ISSN 0236-3941. HERALD of the BMSTU. Series Mechanical Engineering. 2015. No. 2