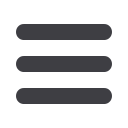

Инструмент для токарной чистовой обработки плазменно-напыленных материалов
ISSN 0236-3941. Вестник МГТУ им. Н.Э. Баумана. Сер. Машиностроение. 2016. № 6
97
Особенно большие трудности при обработке резанием [2, 5] возникают при
изготовлении термоэрозионностойких и нейтронопоглощающих
элементов
кон-струкций изделий из таких плазменно-напыленных материалов и компози-
ций, как ZrO
2
, B
4
C, DyO
3
, Cd
2
O
3
, Sm
2
O
3
, Eu
2
O
3
, Al
2
O
3
+ B
4
C, Al
2
O
3
+ DyO
3
, Cd
2
O
3
+
+
Sm
2
O
3
, Sm
2
O
3
+ W, Eu
2
O
3
+ W, Eu
2
O
3
+ Mo, ZrO
2
+ W и др.
Для обеспечения качества обработки при точении ПМ на основе Al
2
O
3
, ZrO
2
,
B
4
C, DyO
3
, Cd
2
O
3
, Cr
2
O
3
, Sm
2
O
3
, Eu
2
O
3
, Sm
2
O
3
+W разработаны технологические
рекомендации [2, 6–9]. Установлено, что оптимальные значения элементов ре-
жима резания при обработке точением находятся в пределах: скорость резания
v
≤ 0,6…0,75 м/с, подача
S
0
= 0,12…0,25 мм/об и глубина резания
t
≤ 0,15…
0,3 мм. Увеличение до 0,85…0,9 м/с скорости резания
v
сопровождается появле-
нием наклепа, а при
v
> 1,05 м/с имеют место перенаклеп поверхностного слоя,
появление чешуек и шелушение обработанной поверхности. Увеличение глуби-
ны резания более 0,15…0,3 мм и подачи более 0,25 мм/об приводит в отдельных
случаях к выкрашиванию или отслоению напыленной композиции. Шерохова-
тость поверхности зависит главным образом от величины подачи. Однако
уменьшение подачи менее 0,12 мм/об может вызвать повышенную степень
наклепа поверхностного слоя [2, 7–9].
Большое влияние на качество обработки оказывают также геометрические
параметры инструмента. Наиболее рациональными углами заточки режущей
части резцов, оснащенных пластинами твердого сплава ВК8, ВК3, ВК6-ОМ,
ВК6-ОМ с покрытием TiC, ТТ7К12 или резцовыми вставками из эльбора-Р, гек-
санита-Р, ПТНБ, являются: передний угол γ = –10…–5°, главный задний угол
= 6…10°, радиус вершины
r
в
= 1…1,5 мм [2, 9, 10].
Однако оптимальные условия резания ПМ, при которых обеспечивается не-
обходимое качество обработанной поверхности, осуществляются
при очень
низких значениях периода стойкости инструмента: для ранее упомянутых ком-
позиций стойкость твердосплавного инструмента составляет 1…7 мин.
Одним из высокоэффективных направлений повышения периода стойкости
инструмента является разработка методов и средств, основанных на увеличении
длины рабочего участка режущей кромки путем применения в качестве режу-
щего инструмента круглых вращающихся пластин — так называемого ротаци-
онного резания. В настоящее время технологические возможности ротационно-
го резания металлов достаточно подробно изучены и освещены в технической
литературе [11–16]. Однако при резании ПМ применение типовых схем ротаци-
онной обработки и конструкций инструмента не обеспечивает требования к ка-
честву обработанной поверхности: при больших значениях радиуса вершины
резца
r
в
(радиуса круглой вращающейся пластины) резко увеличиваются кон-
тактные нагрузки на обработанную поверхность заготовки, что приводит к об-
разованию недопустимых дефектов: выкрашиванию, частичному отслаиванию и
шелушению материала, появлению сколов, трещин и микротрещин.
Сопоставление оптимальных значений глубины резания (
t
≤ 0,15…0,3 мм) и
радиуса вершины резца (
r
в
= 1…1,5 мм), рекомендуемых при традиционных